Should You Outsource Warehousing? First, Calculate Your Real Warehouse Expenses
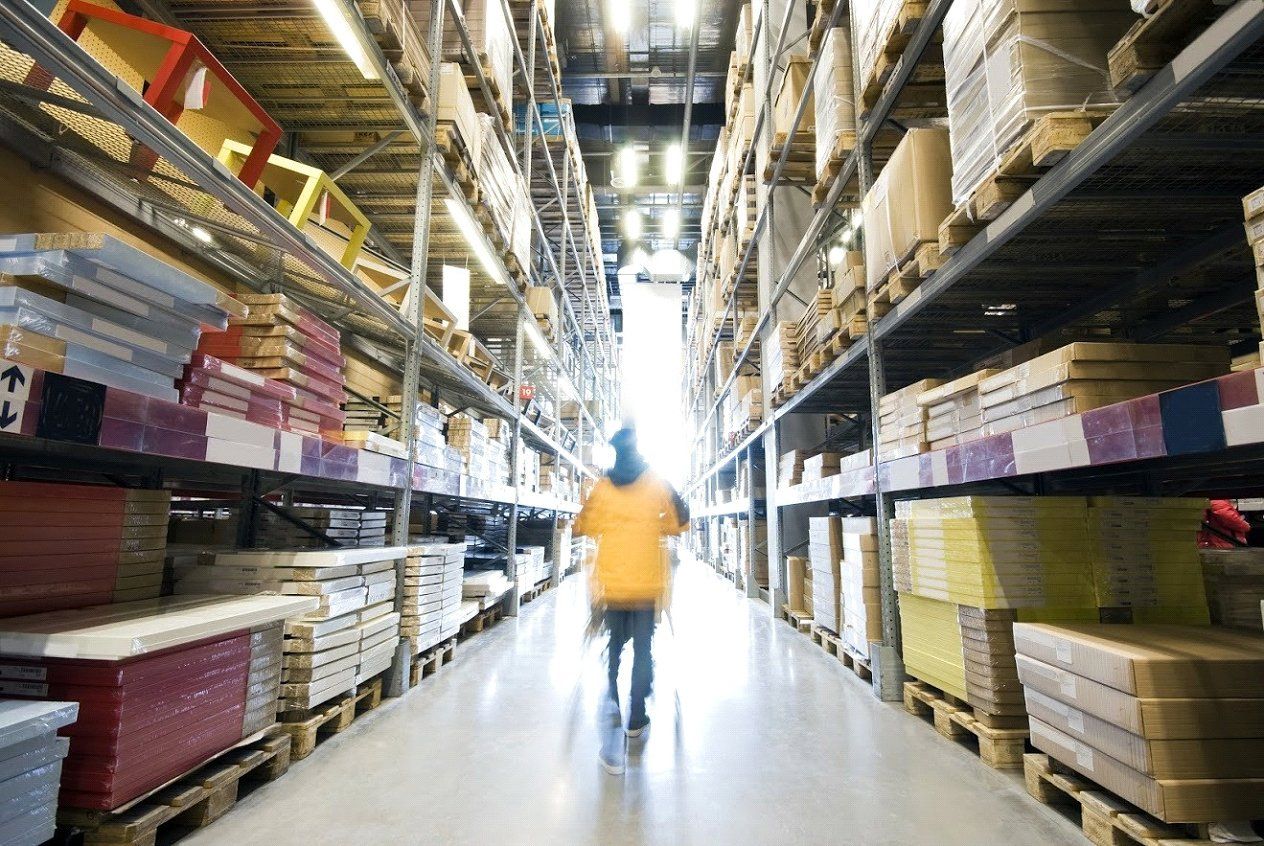
When making the decision between maintaining a warehouse for your goods on your own or paying for an outside service, cost is usually the biggest factor. But to accurately compare costs, you must first be able to add up all the expenses involved in running your own operation. This may sound simple, but determining the full extent of warehouse costs can be tricky.
To help your company get a handle on their expenses, here are the four main categories of warehouse costs and how to calculate them.
1. Storage Costs
The primary purpose of a warehouse is the storage of your goods. These costs are largely made up of storage materials, like racks and pallets and bins, and bills paid over the course of the year to fix and replace these.
You may also include building lease costs in this calculation because storage takes up the vast majority of the building's square footage. Within the lease, you may have fixed costs, such as a base rent payment, as well as operating costs charged by the building owner, which vary.
The good news is that finding and calculating these expenses is usually fairly straightforward. You generally can use information from the company's accounts payable and general ledger as well as invoices from vendors.
2. Handling Costs
Handling costs are what it takes to move goods from one place to another. Start with the financing, leasing, and operating costs of forklifts, pallet jacks, carts, and other large equipment. But by far, the biggest handling expense is the labor involved in moving things around. This labor includes pickers, handlers, receiving and shipping staff, and floor managers.
As with storage costs, handling costs are often fairly easy to identify and calculate. The addition of a lot of labor, though, can be misleading if you fail to capture all the related costs of having an employee on the payroll. Look at things like taxes, benefits, and workers' compensation.
3. Direct Administration
Administrative costs are those which are directly attributable to the warehouse but which aren't necessarily part of the manufacturing process. Insurance, security systems, and maintenance of the warehouse itself are administrative expenses - things you wouldn't have to pay for if the warehouse weren't on-site.
Other administrative expenses commonly used are management of the warehouse, clerical support staff, inventory management software and maintenance, outside consultants and education, and supplies directly used in its operations.
Direct administrative expenses are a little harder to spot because they may be bundled with non-warehouse expenses. But you can easily trace a line from the expense to its clear use in some part of the warehouse's work.
4. Indirect Administration
One easily overlooked category is indirect administrative expenses. These costs aren't always obviously linked to the warehouse but do contribute toward its operations. The payroll department, for instance, handles the administration of payroll to all employees - including warehouse staff. Therefore, a portion of your payroll department's labor may be calculated as an indirect warehouse expense.
Because the expenses are indirect, this category is the hardest to figure out. You may not be able to find actual numbers through the financial books or invoices. Many of these expenses can be better estimated as a percentage of the company's total bill.
Where to Learn More
The more you dig into the costs of running your own warehouse, the easier it will be to decide if outsourcing the warehouse operations could be a profitable move. The other side of the coin, of course, is to price out the various services available through warehousing companies.
At JBS Logistics , we can help. We will work with you to identify ways our warehouse services can reduce or replace costs you are incurring. Armed with this information, you can make the most informed decision possible. Call today to start working with a member of our warehousing team.